You probably know that automating some or all of your manufacturing processes can increase production, reduce waste, modernize your facility, and even boost revenue. But did you know it can help you expand your pool of potential employees and retain your current ones for longer? Let’s examine how automation can enable aging workers and persons with disabilities to carry out industrial and manufacturing work.
Traditionally, as older workers retire, younger ones should take their places, but that simple equation doesn’t always hold true. With increased access to higher education and persistent (if inaccurate) notions of manufacturing work as “dull, dirty, and dangerous,” many manufacturing jobs remain unfilled. “With fewer young people willing to take blue collar jobs, companies must find ways to retain their aging workforce. The median age of employees in manufacturing hovered around 44 years old in 2017, and younger workers remain in short supply as baby boomers edge closer to retirement,” according to Advanced Manufacturing. Clearly, older workers remain a valuable resource.
And, in an effort to fill open positions, and with growing interest in creating diverse and inclusive workplaces, some companies are finding ways to hire people with disabilities. One of the most underemployed groups, disabled people may be able to find work in automation-enabled industrial and manufacturing companies. Industry Week notes that “only 17.5% of people with a disability were employed in 2015, according to U.S. Bureau of Labor statistics. That compares to a 65% employment rate for people without documented disabilities.”
Automation equipment makes these expanded job opportunities possible by making traditionally manual, physical labor more ergonomic and adaptable to changing needs of employees. The keys are to be strategic and prioritize safety.
Understanding human factors
As we age, and especially as we pass into and beyond our 50’s, we experience gradual decline in strength, dexterity, speed, coordination, and endurance. These change a worker’s ability to remain standing for a shift, work with hand tools, lift and carry objects, and even maintain consistent output volume and quality. Similarly, those with disabilities may have limited dexterity, grip strength, mobility, capacity to reach for or transport items, ability to hear auditory clues in the environment, etc.
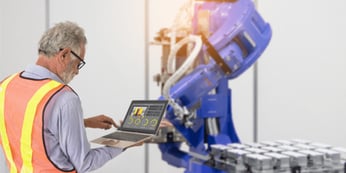
These challenges contribute to fatigue, repetitive stress, injury, and poor production, but equipment like collaborative robots, motorized equipment, and conveyors equipped with sensors and sophisticated software are able to compensate for many of these situations. “Some examples are musculoskeletal disorders due to repetitive or awkward motions, or traumatic injuries (for example, in poultry processing, where cuts are common). They can also prevent multiple hazards in emergency response situations such as chemical spills,” says Vladimir Murashov, of the National Institute for Occupational Safety and Health (NIOSH). The bottom line is automated equipment creates more than one way to get a job done and enables a greater number of workers do it.
“Automated equipment creates more than one way to get a job done and enables a greater number of workers do it.” Tweet this
Automation as accommodation
Collaborative robots, or cobots, are an excellent example of accessible high-tech equipment. When configured for specific applications, cobots can make tasks easier and remove barriers to productivity. For example, a robotic arm can be programmed to do much of the lifting, rotating, and positioning of parts, reducing repetitive motion stress and freeing the worker to do detail work. Another option is fitting cobot arms with end of arm tools (EOAT) for tasks like driving screws, which can be challenging when dexterity and grip strength are limited.
Flexibility is another important factor in accommodation. Some cobots can be programmed to run in a “reduced safety” mode, increasing speed and capacity when operators are out of range and returning to regular, slower speeds when the worker returns.
Cobots aren’t the only types of equipment that can improve ergonomics and reduce fatigue. Transporting assemblies, boxes, or tools by hand or even with a push cart is a challenge for workers with impaired mobility or reduced stamina. Adding motorized carts, hoists, conveyors and similar equipment eases the burden while still allowing the person to do the actual production work. Similarly, power adjustable work surfaces that adjust to different heights reduce or eliminate the need for stooping, reaching, or prolonged standing.
Risk assessment remains critical to safety
Safety is always critical with automated equipment, perhaps even more so when workers may move more slowly or with less precision. Writing in Machine Design, Ryan Braman notes, “when designing a collaborative robotic cell, engineers must take into account the intended application of the cobot and the environment it might be placed in, then develop a safety plan for each use case.”
Most cobots employ the following safety features, which help minimize workers’ risk of injury:
- safety monitored stop (function stops until the operator resumes the machine)
- hand guiding (operator manually moves the arm to program a set of movements, customizing its path)
- speed and separation monitoring (vision sensors track the worker’s position and adjust working speed to preset parameters)
- power and force limiting (movement stops when sensors detect an overload of force in the arm’s joints and at other points; rounded edges and enclosed motors dissipate force and limit contact with dangerous components)
Braman says “a proper risk assessment identifies all of the ways a human and a robot could potentially come into contact with each other, evaluating the associated level of risk, and mitigating that risk using appropriate measures.” ISO and RIA standards further detail procedures for safety tests, including transient contact, where human and robot approach each other and then move apart, and quasi-static testing, which measures the force applied when objects are constrained against each other (i.e. pinching or grasping).
Thanks to sensors and vision technology, PLCs and other motion controllers, and high-speed communications between devices, current automation equipment can be programmed to be highly responsive in real time.
While industrial and manufacturing companies do still need to find ways to attract younger workers, they can also find ways to expand and retain their workforce through automation. At Force Design we have the expertise to adapt many processes and equipment to a wider range of workers. Please contact us to learn how.
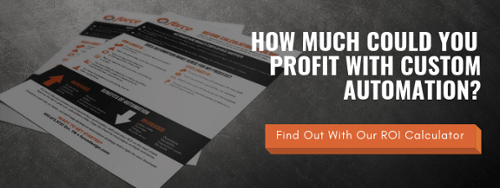