If you’re a small or medium-sized manufacturer and your throughput, labor force, and component quality are optimal and continuously improving, don’t bother reading any further. But if you have any challenges in these areas, and if you’ve ever wondered how to address them effectively, we may have some ideas for you.
Still there? When you think of automation in manufacturing it may seem like a no-brainer. As in, there is no way this will work in our shop, we can’t afford it, and we wouldn’t even know where to start. Especially if you tend to think of enormous, lumbering robotic arms, fencing, and production areas the size of football fields, you may be surprised to see some of the more recent developments in automation equipment that put it well within reach of businesses like yours. Here are some points to consider.
What are your challenges?
Before you think too much about what types of equipment would work in your facility or what you can afford or have space for, take a close look at any operations or production challenges you’re experiencing. Don’t worry about how to fix the problems with robotic arms or elaborate systems of conveyors. Focus on the problems you’re having and what’s causing them. Possible examples include:
- low or reduced throughput
- inability to fill orders on time
- high rates of scrap and/or rework
- part quality or inspection issues
- inconsistent or high use of consumables
- labor shortages including finding, replacing, or retaining employees
- production bottlenecks
- safety risks (dangerous or fatigue-causing tasks)
- accommodating planned expansion or production changes
Remember to look at the full production process, since problems can be caused by things happening down or upstream. The goal is to identify the root cause of the challenge. For example, the slowdown at the lathe or the welding station may originate two stations back with material supply storage, but it isn’t noticed it until this cell.
What are the options?
Look for examples of manufacturing automation in action to see what’s possible and how machines can be coordinated to work together. At this stage, try not to dismiss options if they don’t precisely fit your situation – it’s often possible to build a custom solution or configure an off the shelf or pre-engineered system to meet your needs.
Swapping out manual processes for automatic (or semi-automatic) ones can have far-reaching effects by moving supplies faster, reducing finishing work, quickly inspecting large quantities of parts, or even sorting items. Some common starting points include:
- packaging and palletizing
- tending CNC and other machines (e.g. opening hatches, pressing buttons)
- material handling (e.g. loading and unloading, supply retrieval)
- welding
- grinding, drilling, or other material removal or finishing tasks
- sorting
- “pick and place” operations
- part inspection and testing
- assembly
- dispensing or applying materials, dipping parts (e.g. glue, paint, coatings)
- labeling
- conveyance
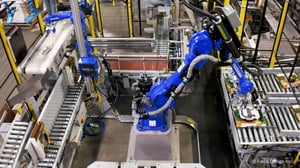
Automation doesn’t have to be an all-or-nothing proposition. Thanks to compact robots with built-in safety features, you can have a mix of robotic and manual tasks in the same work cell or production line. For example, a machine can be loaded by a worker, machined by an automated lathe, then unloaded and inspected by worker and placed on a conveyor to move it to the next station.
It’s also not a one-to-one substitution where a machine does the same tasks the same way humans did, only faster. In fact, you may be able to change or eliminate steps, reorder processes, or gain efficiencies as a result of automating.
How will our work and culture change?
It’s no surprise that adding more machines and robotic arms will make your facility look and sound different, but there are changes to work and company culture to anticipate too. Helping employees buy into the efficiencies and other benefits is critical to a successful transition. Some things to plan for include:
- changes to roles, not elimination of jobs – operators monitor machines and keep them running rather than doing the manual labor
- adding computer, problem solving, data analysis, and troubleshooting skills to workers’ existing expertise
- preparing for the effects of faster cycle times on prior and later workstations or stages of production – adapting supply chain or end-of-line processes to accommodate the changes
- training operators on troubleshooting, basic maintenance, and programming robotic arms by hand-guiding
- addressing operator’s concerns about being replaced by a machine by emphasizing the shift in the nature of the work and opportunities to learn more skills
Can we afford this?
It takes time, a dedicated internal team, and often outside guidance to identify your challenges and figure out how automation may be able to solve them. Once you’ve started to visualize what’s possible, it’s time to take a step back, justify the costs, and prove out a realistic ROI calculation. We suggest taking a broad view that encompasses the far-reaching effects of automated processes, for example:
- increased throughput and production – keep up with demand, expand production, or fill larger orders in the same or less time
- enhanced worker safety – reduce exposure to fumes and dangerous operations, avoid fatigue or injury with ergonomic equipment and less physically demanding tasks, minimize risk of injury with built-in safety sensors and devices
- improved worker engagement – reduce monotonous tasks so workers can focus on managing the machine’s workflow, increase responsibility with easy programming features
- redeployment of robotic arms to different cells around your facility for a range of tasks and part families – multi-axis movement means and many tooling options means arms can run several programs for flexible use
- more efficient low volume-high mix manufacturing – program a single machine to make variations of a part based on changing needs for your assemblies or what your suppliers need, quickly switch out production if you do not run a single component for a full shift or day
- economical, efficient use of consumables and raw materials – precision of machine-based operations means movements and material use is highly regulated for more parts made to spec and less scrap
- data-driven decisions – “smart” machine data collection and analysis lets you check parameters and cycle times and make adjustments on the fly to optimize processes
- efficient use of space – compact collaborative robots require minimal guarding/fencing for safety and can be mounted on mobile platforms or a tabletop for easy access and proximity to other workstations
The bottom line? ROI includes more factors than just the direct monetary value of a piece of equipment – every little change resulting from automation adds up.
As you explore the possibilities automation and robotics offer, keep in mind you really do have the expertise you need already: it’s in your manufacturing experience, your workforce and the skillsets they bring to the table, your detailed knowledge of processes up and downstream, and your ability to predict where changes might improve bottlenecks. These are the keys to developing a custom solution. All that’s missing is a partner to show you the options. There are probably several creative solutions depending on your needs, application, and budget. We’d be happy to show you how to get started (we even have an ebook about it!). Please contact us to learn more.